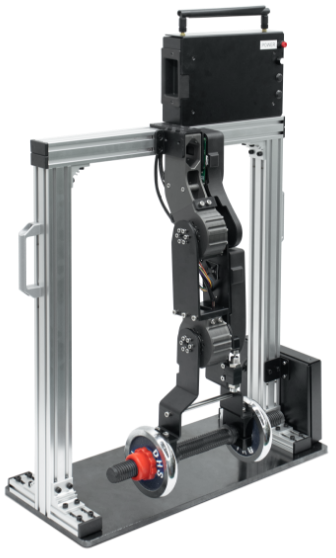
Robot Control Experimental Device with reinforcement learning
To allow direct experience and experimentation with force mode control systems and controllers based on artificial intelligence, we offer the control experiment device (angel KIT CE10).
angel KIT CE10 features a leg-shaped structure with a pair of Angel Robotics' wearable robot actuators (angel KIT AM10) and motor drivers (angel KIT MD10) linked together, with the capability to attach additional weights at the end-effector. It also includes a high-performance AI module, enabling the implementation of artificial neural network algorithms.
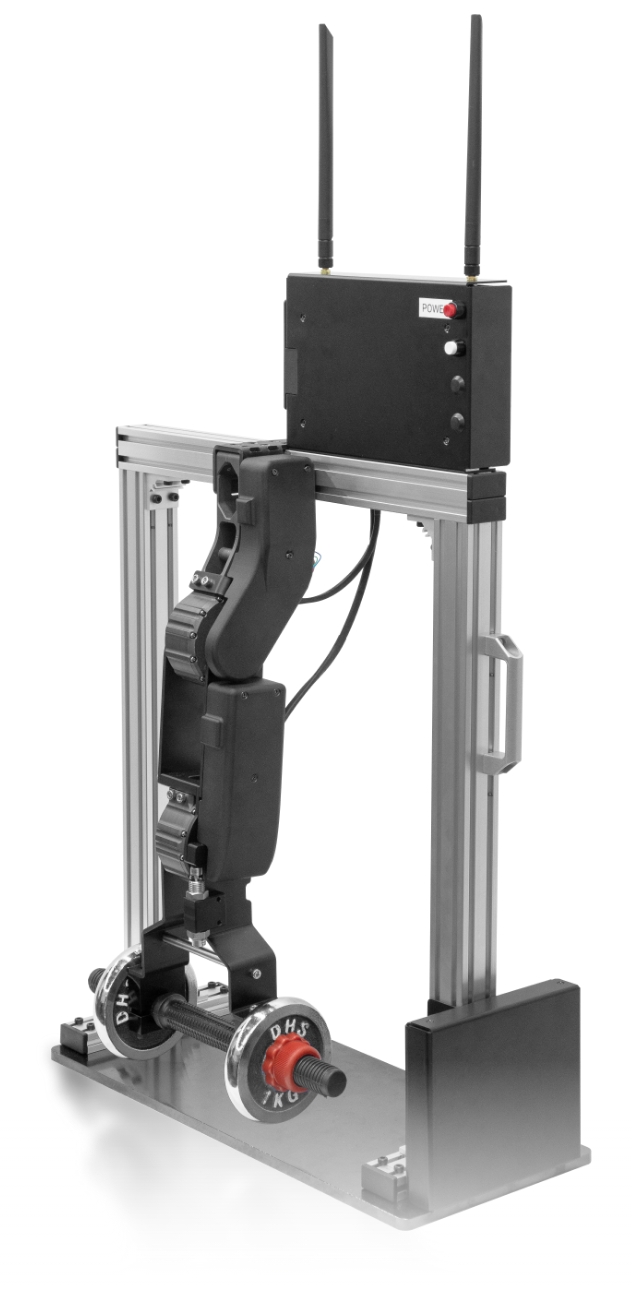
What types of control learning and practical applications can be achieved with angel KIT CE10?
- Robot joint control based on embedded systems
- Actuator control interacting with sensors
- Joint trajectory implementation using position control
- Resistance sensation reduction in joint movements through gravity compensation control
- Smooth robot control via impedance control
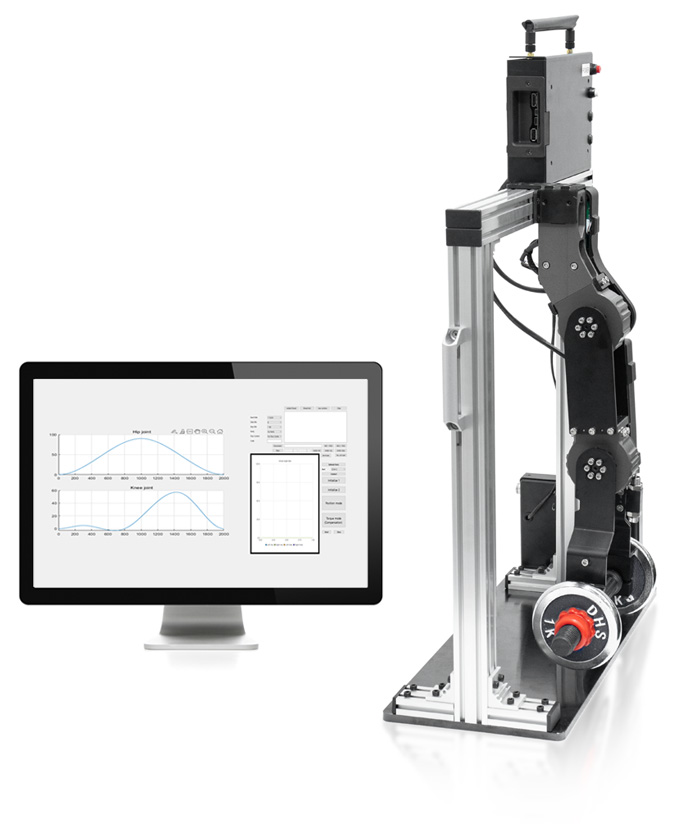